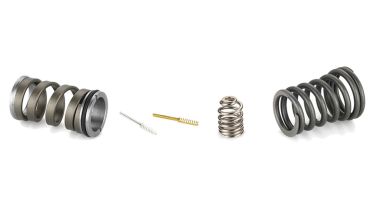
Innovation and Precision in Custom Springs: RPK Group at the Service of Global Industry
RPK Group, a leader in custom spring manufacturing for multiple industrial sectors
For more than five decades, we at RPK Group have established ourselves as leaders in manufacturing custom springs for a wide range of industrial sectors. Our dedication to innovation, combined with an unwavering commitment to quality and precision, has enabled us to meet the most demanding needs of our clients in diverse industries such as medical devices, electrical, automotive, industrial, power tools, consumer goods, e-mobility, and more.
At RPK Group, we understand that each sector has unique requirements for its spring applications, from the rigorous standards of hygiene and durability in the medical sector to the demands for strength and efficiency in the automotive industry. Therefore, our team of highly trained engineers and technicians works with each client to design and manufacture springs that meet their specifications and technical requirements.
Custom Spring Manufacturing Process
The custom spring manufacturing process is both an art and a science, combining technical precision with specialized knowledge in materials and mechanical design. Below is a step-by-step outline of this crucial process for producing custom springs:
Design and Initial Specifications
Everything begins with the client’s specifications and spring design requirements. Engineers work closely with the client to understand the intended use of the spring, the environmental conditions it will be exposed to, the loads and cycles it must withstand, among other factors. Using computer-aided design (CAD) software, a virtual model of the spring is created, serving as the basis for manufacturing. Additionally, these are verified through FEA/FEM analysis processes.
Material Selection
Material selection is crucial and depends on several factors, such as the necessary strength, durability, ability to withstand repetitive stresses, electrical conductivity (in some cases), and corrosion resistance. Common materials for spring manufacturing include carbon steel, stainless steel, titanium alloys, copper, among others.
Manufacturing Process
- Material Cutting: The material is cut into wire or bar form according to the design dimensions and specifications.
- Coiling/Forming: The wire undergoes coiling or forming processes in specialized machines with specific tooling for each spring. This can include bending, stretching, forming, or coiling, depending on the type of spring being manufactured (e.g., compression springs, extension springs, torsion springs, etc.).
- Heating: In some cases, especially when working with high-strength steels or harder materials, the material may undergo heat treatment to improve its mechanical properties.
- Pre-stressing: Some springs, especially those operating under high load conditions, may be pre-stressed to enhance their strength and durability.
- Finishing: Terminal ends are added to the spring according to the design specifications. This may involve forming hooks, loops, or any other type of termination that allows for proper installation or connection of the spring in its final application.
- Surface Treatments (Optional): Surface treatments like anti-corrosion coatings, lubricating coatings, or surface treatments to improve fatigue resistance can be applied.
Inspection and Quality Control
Throughout the manufacturing process, comprehensive unitary quality controls are conducted to ensure that the spring meets design specifications. This can include precise dimensional measurements, strength tests, metallurgical analyses to verify material integrity, and load tests to simulate real-use conditions.
Packaging and Delivery of Custom Springs
Once the springs have passed quality controls, they are packaged according to the client’s instructions. This may include special protections to prevent damage during transportation or adaptations to assembly lines. Finally, the springs are shipped to the client for installation in the final application.
Innovation and Technology in Spring Manufacturing
Spring manufacturing has significantly evolved with technological advancements. Automation and the use of CNC (computer numerical control) machinery have improved the precision and efficiency of the process. Additionally, computer simulation and predictive modeling allow engineers to optimize spring design to maximize performance and lifespan.
In summary, the spring manufacturing process is a prime example of how engineering and metallurgy combine to create essential components for a wide range of industries. From initial design to final delivery, every step is crucial to ensuring that springs meet the highest quality standards and fulfill the specific needs of each industrial application.
Diversity of Applications and Sectors Served
Our experience spans a wide variety of industrial sectors:
- Medical Device Sector: We manufacture springs that meet the highest quality and sterilization standards, essential for medical devices and precision equipment.
- Electrical Sector: We supply springs for applications in electrical and electronic components, ensuring conductivity and reliability.
- Automotive: We produce springs that withstand severe conditions of temperature, vibration, and load, essential for suspension systems, braking, and more.
- Industrial: We provide robust spring solutions for heavy machinery, ensuring safe and efficient operation in demanding industrial environments.
- Power Tools: We design springs that enhance the performance and lifespan of electric and pneumatic tools, optimizing precision and power.
- Consumer Goods: We manufacture springs for consumer products that require strength and reliability, improving the end-user experience.
- E-Mobility: We support the transition to electric mobility with springs designed for applications in electric vehicles and charging systems.
If you are looking for a trusted provider for your custom spring needs, do not hesitate to contact us at RPK. We are here to turn your ideas into reality with spring solutions that make a difference.
Commitment to Quality and Innovation
Quality is the fundamental pillar at RPK. We use cutting-edge technologies and advanced manufacturing processes to ensure the dimensional precision, structural strength, and durability of our custom springs. From initial design to final production, every phase of the process undergoes strict quality controls to ensure that our products exceed our client’s expectations and perfectly fit their specific applications.