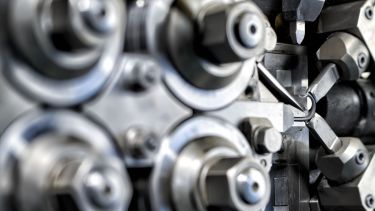
The Spring Manufacturing Process at RPK: Quality and Precision at Every Step
RPK Group has over 50 years of experience in high-quality spring manufacturing
At RPK Group, we have worked for over 50 years with a spring manufacturing process that meets the most demanding quality standards. We understand that springs are essential to ensure the optimal performance of numerous automotive, medical, electrical, and industrial products. Each spring is meticulously designed, developed, and industrialized through a rigorous process that combines our extensive experience with cutting-edge technology, ensuring precision, durability, and adaptability to each customer's needs.
At RPK Group, we want to share insights into our spring manufacturing process, drawing from years of experience from our engineers and our RPK Technological Center in producing springs, dynamic stamped and bent parts, and assemblies.
Our spring manufacturing process is structured into three fundamental stages: design, product and process development, and spring industrialization. Each stage is crucial in ensuring the quality and precision of our springs.
With this structure, we aim to provide you with a clear and complete view of how we manufacture high-quality springs that meet our customers' expectations in various sectors, including automotive, medical, consumer goods, and more. Contact us, and we will create your spring from scratch or enhance the performance of your existing components and designs.
Spring Design: The Key Lies in Planning
RPK Group's spring manufacturing process begins with a meticulous design phase. We use advanced simulation tools and 3D modeling to create a customized design, ensuring that each spring is tailored to its specific purpose and built precisely.
Three key pillars support our spring design process:
- Engineering
- Reverse engineering
- Material specialization
Our product engineering team also works closely with customers to define exact specifications: What resistance level is required? What shape and size optimize performance in the customer's specific application? Every detail is carefully considered to ensure the spring's efficiency and reliability.
This collaborative approach allows us to anticipate potential challenges and find solutions before entering the production phase. Moreover, using virtual simulations, we can predict the spring's behavior in real-use scenarios, minimizing errors and ensuring excellent quality from the first prototype.
We also enhance the performance or characteristics of existing components to meet our customers' needs better.
At the same time, our product engineers work alongside the development team to ensure the most efficient production.
Spring Development: Turning Design into Reality
Once we have a solid design, we move into the development phase, where theory becomes practice. At RPK Group, we have a specialized workshop and state-of-the-art machinery that enable us to produce prototypes with great speed and precision.
At this stage, we subject prototypes to rigorous tests to assess durability, fatigue resistance, and performance under different pressure and temperature conditions. Each prototype is analyzed and adjusted until it meets the defined specifications. This spring manufacturing process ensures that the final product meets and exceeds our customers' expectations.
Our commitment to quality is unwavering. We refine every prototype until it is ready for mass production, ensuring that each spring, whether for the medical, automotive, or consumer goods industry, meets and exceeds our customers' expectations without compromising performance or safety.
Our spring manufacturing process includes:
- FEM/FEA analysis: We closely collaborate with your engineering teams to develop components for highly dynamic applications, creating digital models of different proposals to ensure they fit perfectly with your product.
- Advanced Product Quality Planning (APQP) and prototyping: A fast and realistic process, including 3D printing, to test performance in real-world environments. We develop prototypes quickly, including 3D-printed parts, to evaluate performance and assembly in a working environment. In some cases, our Technology Center is involved in the development process.
- In-house machine and tooling design and development: CNC machines, R&D, testing, controls, maintenance—our in-house workshops handle it all.
- Spring cleaning and packaging: Our dedicated department ensures that your spring manufacturing process meets your cleanliness and production requirements.
Processes and Industrialization: Large-Scale Quality
Once a prototype is approved, it's time to scale up to mass production—a phase requiring precision and efficiency. At RPK Group, we have developed a production system that ensures each spring meets the same quality standards as the initial prototypes, regardless of the production volume.
Our highly skilled production teams operate specialized, state-of-the-art machinery to ensure fast and error-free manufacturing. Additionally, each production line has unitary inspection and control systems that detect irregularities before the product leaves the factory. This guarantees that every spring delivers the expected performance and durability.
At the end of this phase, we implement rigorous quality controls, including resistance testing and precise measurements, ensuring every spring complies with international standards and surpasses the specific requirements of demanding sectors such as automotive and medical.
Key Processes in Spring Manufacturing:
- Complete manufacturing in Europe, America, and Asia
- Ramp-up
- Technical and biological cleaning in clean rooms
- ISO 7 clean rooms in Europe and Asia, with ad hoc clean room creation for special projects
- Complete packaging in clean rooms
- Passivation
- 100% integrated unitary control using vision and control technology
- Custom-built automatic assembly lines
- State-of-the-art laser welding
- Deburring
- Grinding
- Vibrating
- Hot and cold presetting and hot setting
- Oiling
- Demagnetization
- Special coatings and surface treatments
- Heat treatments
- Shot peening
- Laboratory product testing: environmental, fatigue, relaxation, cleanliness, residual analysis, dynamic testing, etc.
At RPK Group, every spring we manufacture is a testament to our dedication and expertise. We understand that our customers seek a product that meets their technical requirements and offers a long service life and unparalleled reliability. Thanks to our design, development, and industrialization processes, we manufacture high-quality springs tailored to the needs of each customer and industry.
Whether your company operates in the automotive, medical, power tools, consumer goods, or other industries, RPK Group is ready to be your trusted partner in the spring manufacturing process.
Contact us for any inquiries.