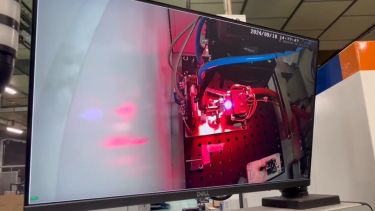
Enhancing the Welding of Flexible Copper Busbars with BrightLine Laser Technology
RPK Group incorporates TRUMPF's precision laser welding for efficient, high-quality results in electric vehicle power systems and many other applications
By Iker Ibisate, RPK Technological Center,
The RPK Group, through its adoption of TRUMPF's BrightLine laser welding technology, offers groundbreaking advantages in the welding of flexible copper busbars. These components are essential for energy distribution in electric vehicles, where precision and efficiency are critical. BrightLine laser welding stands out for its high precision, lower heat input, and superior speed, providing excellent weld quality while maintaining the mechanical and electrical properties of copper. This advanced method not only optimizes production efficiency but also ensures consistent, high-quality results, making it the ideal choice for industries requiring reliable and effective electrical systems.
TRUMPF's laser
Advantages of laser welding with BrightLine by Trumpf:
- High precision
The BrightLine process with a 24-micron PFO is optimized to achieve extremely precise welds, which is crucial in applications where the integrity and conductivity of copper are essential, even with sheet thicknesses as small as 0.1mm. The geometric deformation of the BusBar and the heat-affected zone are minimized, preserving the mechanical and electrical properties of the copper, as well as the integrity of the coatings.
- Lower Heat Input
Unlike traditional welding methods, the incorporated BrightLine laser allows energy densities of up to 6kw concentrated in a very small point, minimizing the heat affecting surrounding areas. This is especially beneficial in copper, which tends to dissipate heat quickly, complicating other welding methods. The lower heat input avoids distortions and helps maintain electrical properties without damaging coatings, like Tin or Nickel.
- Higher Welding Speed
The BrightLine system enables fast and efficient welding of up to 200mm/second. This is crucial in manufacturing busbars, which are often repetitive elements in mass production. The high energy deposition rates of the laser allow for reduced cycle times compared to other methods, improving production efficiency and thus lowering costs.
- Improved Quality and Repeatability
The laser process offers excellent repeatability, which is important in the manufacturing of FLEXIBLE busbars, where multiple consistent welds are required with 2-micron precision. The BrightLine technology provides fine control over the process, ensuring each weld is consistent in quality, free of common defects like cracks, pores, or inclusions, even with pre-coated materials such as Tin and/or Nickel.
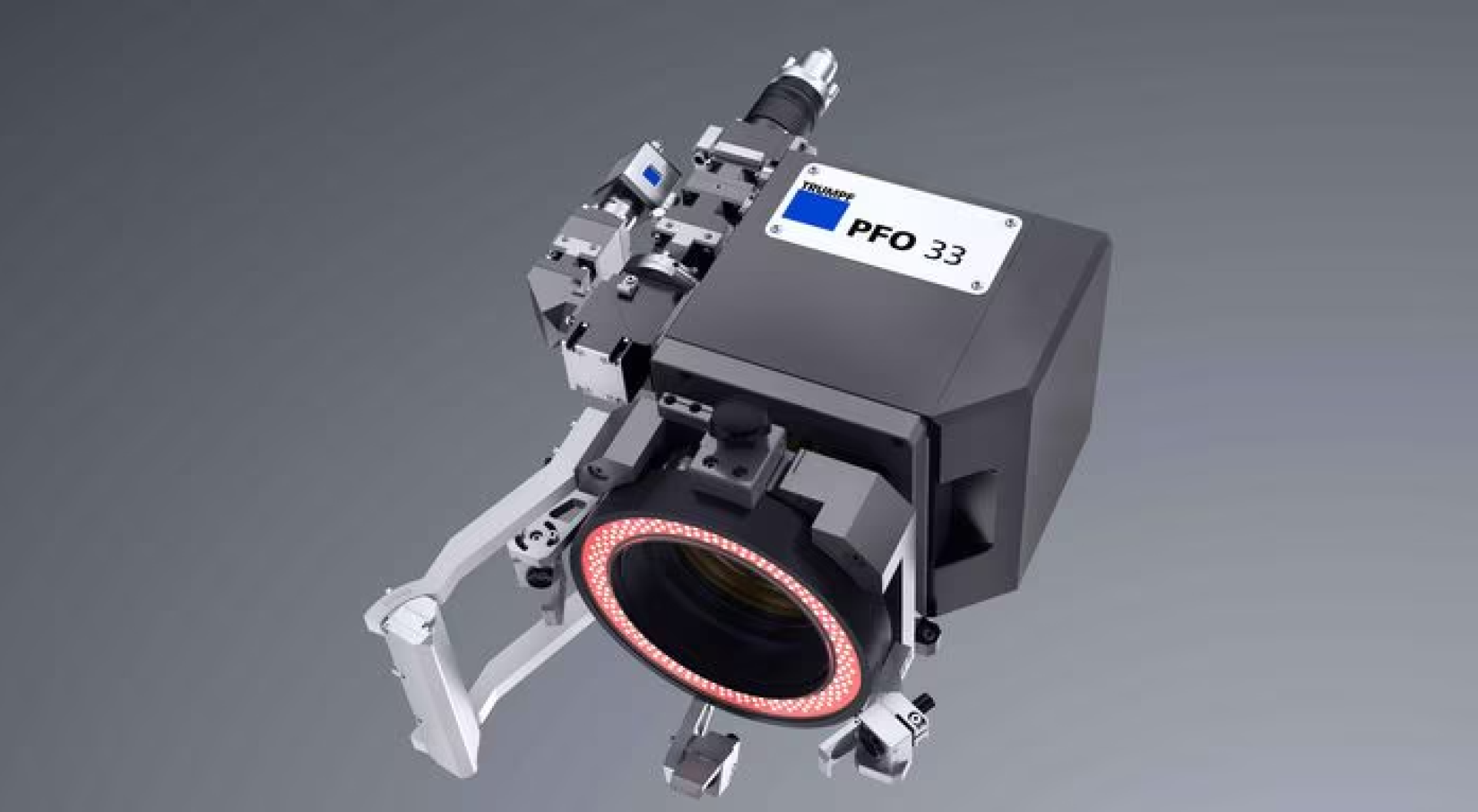
- Joining Difficult Materials
Busbars may involve joining copper with other materials, such as aluminum or pre-coated sheets. The BrightLine laser technology can handle these combinations with precision, avoiding issues such as improper fusion or the formation of undesirable intermetallics.
- Less Post-Processing Needed
Due to the precision and low thermal input, the welds require less cleaning or finishing afterward. There is no need to remove additional material or correct deformations, saving time and costs.
- Compatibility with Automation
The incorporated laser welding is integrable into automated systems, ideal for mass production lines of busbars in the automotive industry. With the BrightLine system, components can be welded automatically with high precision, reducing the need for manual intervention and improving overall productivity.
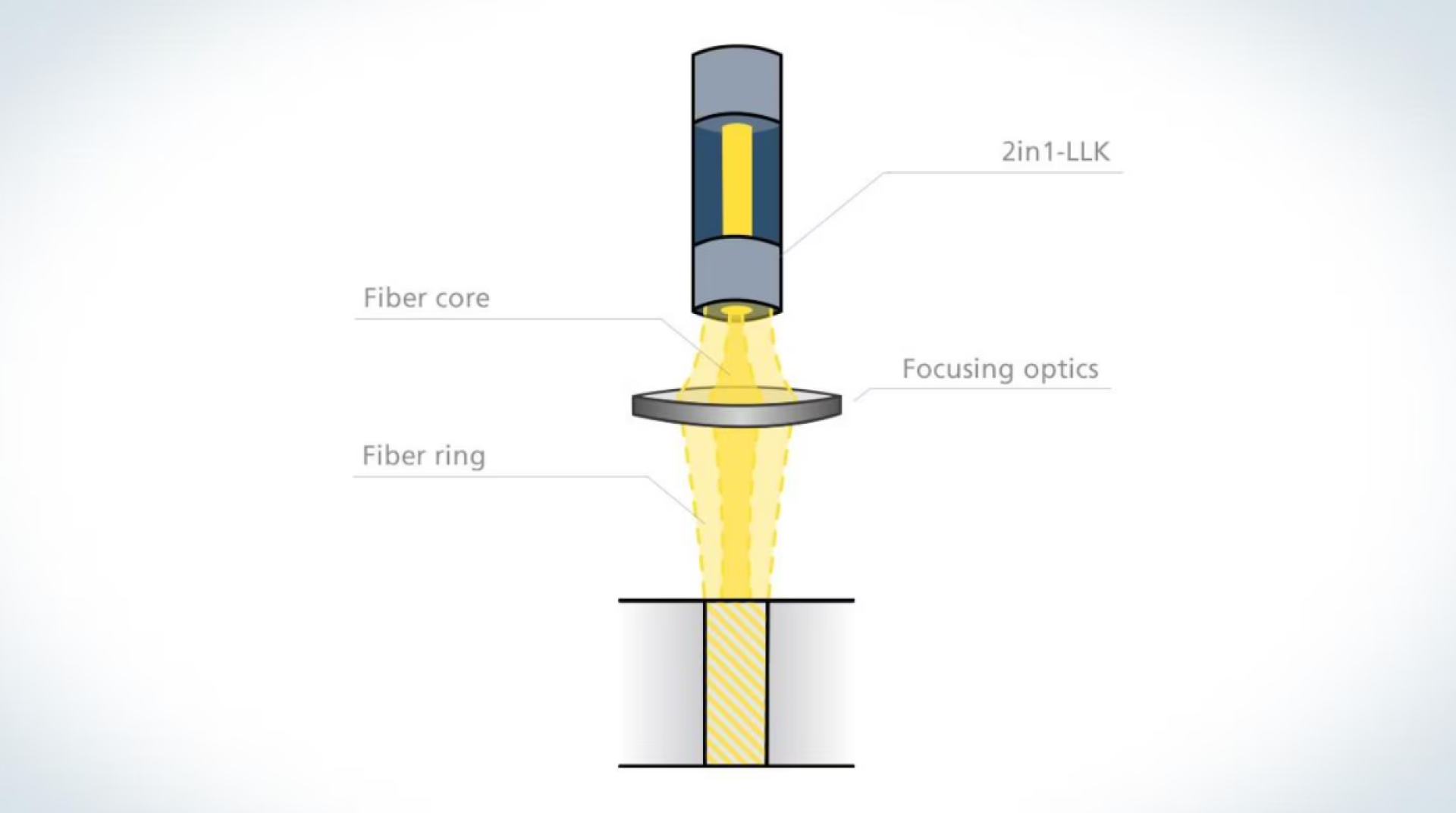
- Reduction of Waste and Filler Materials
The BrightLine laser can weld without the need for filler materials or controlled atmospheres, simplifying the process and reducing costs. Additionally, material waste is minimized, making it more resource-efficient.
- Aesthetic and Compact Welds
The BrightLine laser generates clean, aesthetically pleasing welds, which is an added value in applications where busbars are exposed or visible, such as in high-performance electrical components or electric vehicles.
- Low Electrical Resistivity in the Joint
One of the most important requirements for busbars is ensuring low resistance at the joints to avoid energy losses. Welds made with the BrightLine laser achieve high-quality joints with low resistivity, improving the electrical efficiency of the system.
The BrightLine TRUMPF´s laser welding is an optimal solution for the manufacturing of copper busbars due to its high precision, low heat input, speed, and weld quality. This makes it the most competitive option for industries seeking reliability, precision, and efficiency in their electrical distribution systems.